Mycelia House

Caity Duffus, the Carl Nielsen Design Accelerator recipient for 2024, is bringing mushroom growing home with her design prototype for Mycelia House as part of her vision for a sustainable fungi network.
During her nine-month Carl Nielsen Design Accelerator program in 2024, Caity Duffus set up a studio with a ceramic 3D printer to prototype the design for Mycelia House, a terracotta vessel with holes that allow the natural growth of mushrooms. Under the guidance of industrial designer Ed Ko, she made and tested 17 prototype vessels, various plates and lids, and collaborated with mushroom growers at Ruffle Farm and Nick Ritar from Milkwood on the substrate grow bag system.
Duffus’ long-term goal is to promote the important role of fungi in our ecosystem and to challenge perceptions of them as poisonous, reframing them as beautiful and sustainable. In the following interview, Duffus spoke with Powerhouse Collection curator Angelique Hutchison about her experience on the program as she readied Mycelia House for market.
‘Fungi is the largest living organism on our planet. As humans, there’s a lot we can learn from their way of being,’
Prototyping Mycelia House
Angelique Hutchison: What was your intention with the accelerator program?
Caity Duffus: The main goal of the program was to develop the design of Mycelia House into a commercial scalable solution. I wanted to work closely with mushroom growers to validate and refine the system. Ceramic 3D printing is still fairly new, so this meant purchasing a machine for the prototyping and production process.
Another big goal was related to sustainability. I hope Mycelia House can open us to a new relationship with the fungi kingdom through displaying, caring for and eating mushrooms.
I wanted to commit to trusting in the design process. I went back to using CAD [computer-aided design] and had to relearn the programs. Another goal was to photograph each stage to be able to tell the story of how the product evolved and came to life.
Aligned relationships were really important, connecting with people in a way that felt open and curious and building community around it. I’ve reached out to a lot of people in the 3D-printing community, here and overseas, and to other people in the mushroom-growing community to get a sense of the industry, meeting people doing great things and building my skills in those areas.
I was also thinking about how I could move in the same way as fungi. The values I created for the business were centred around this and themes like care and listening, and treating design like a gardening practice.
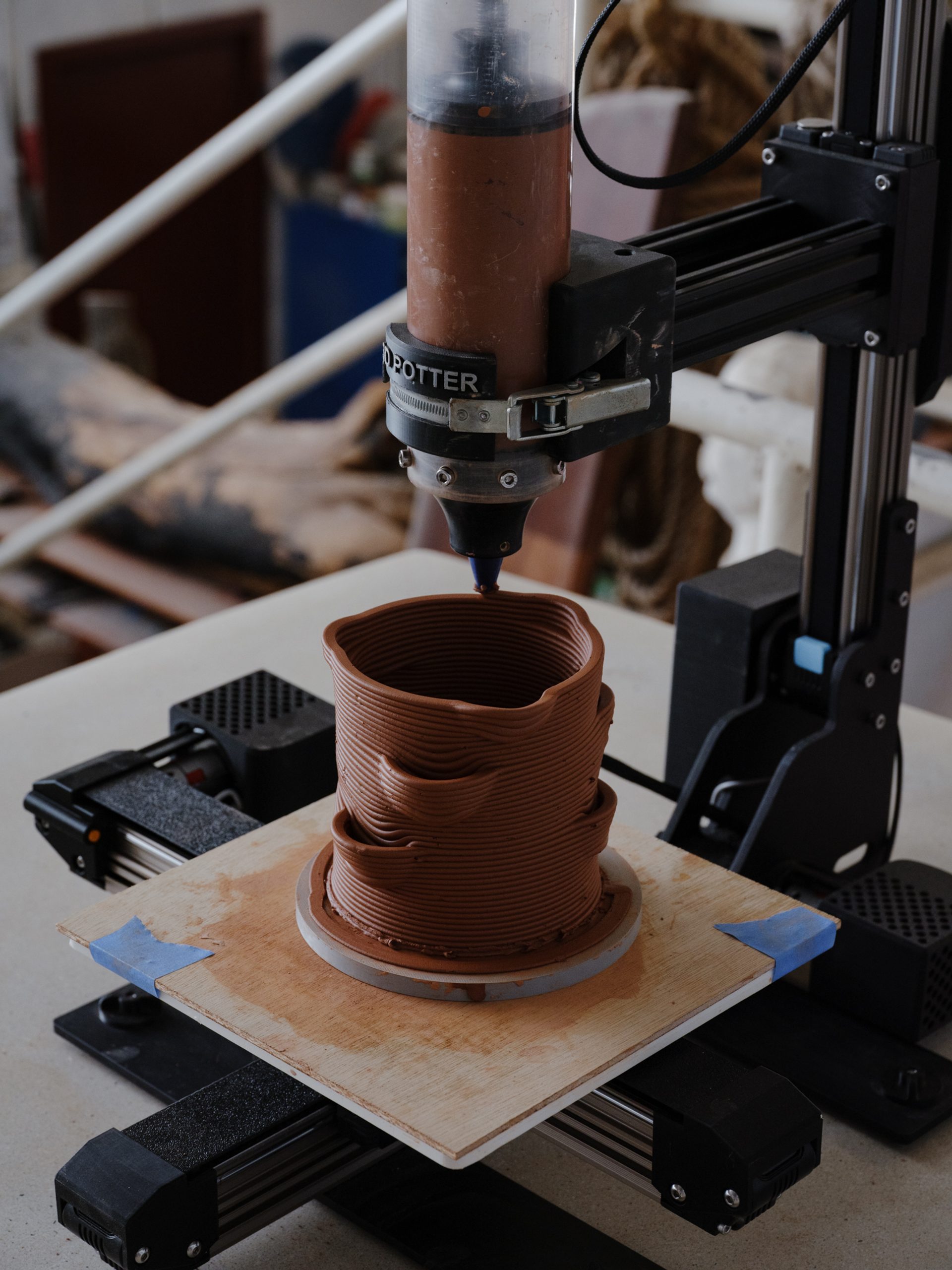
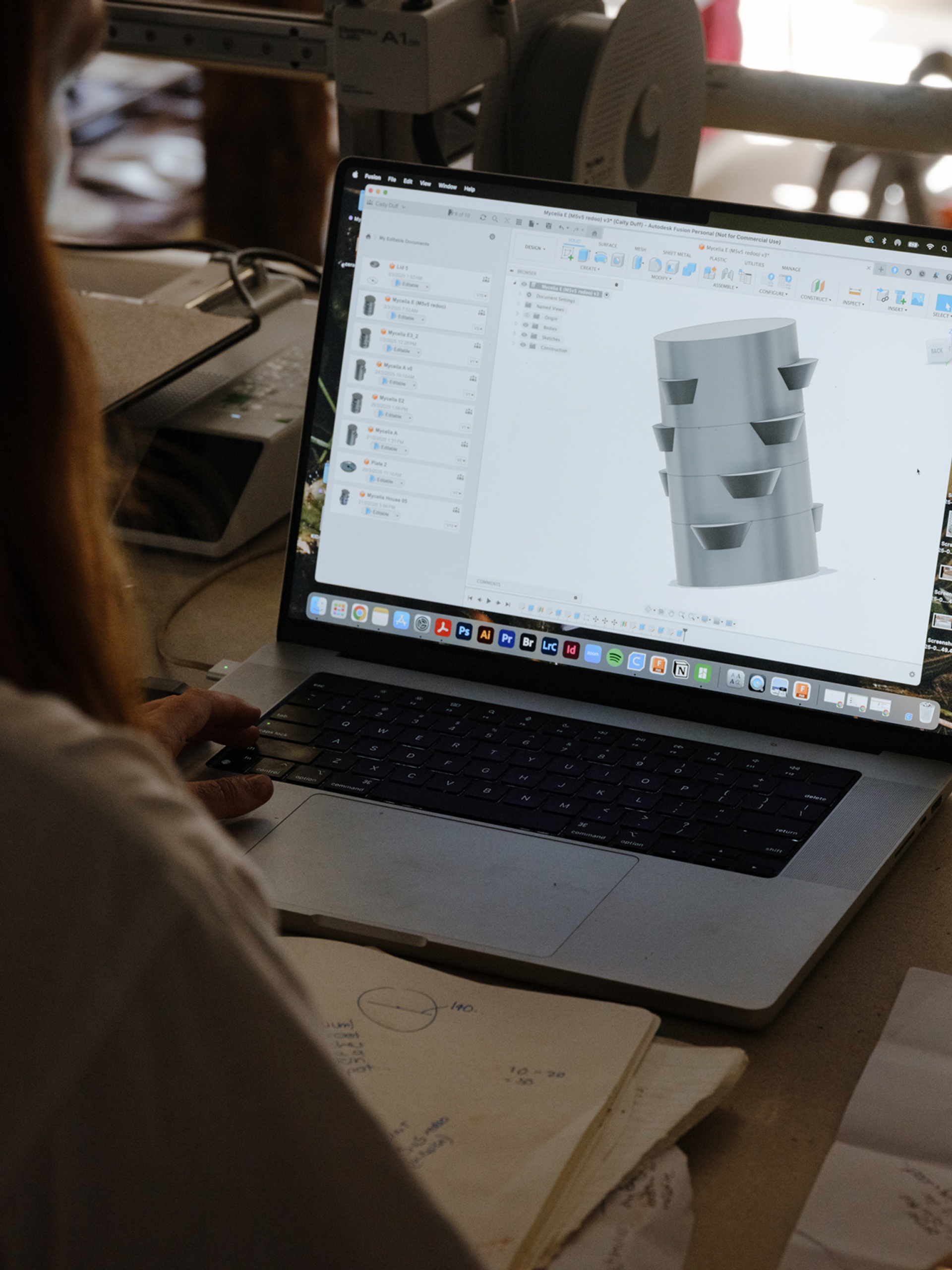
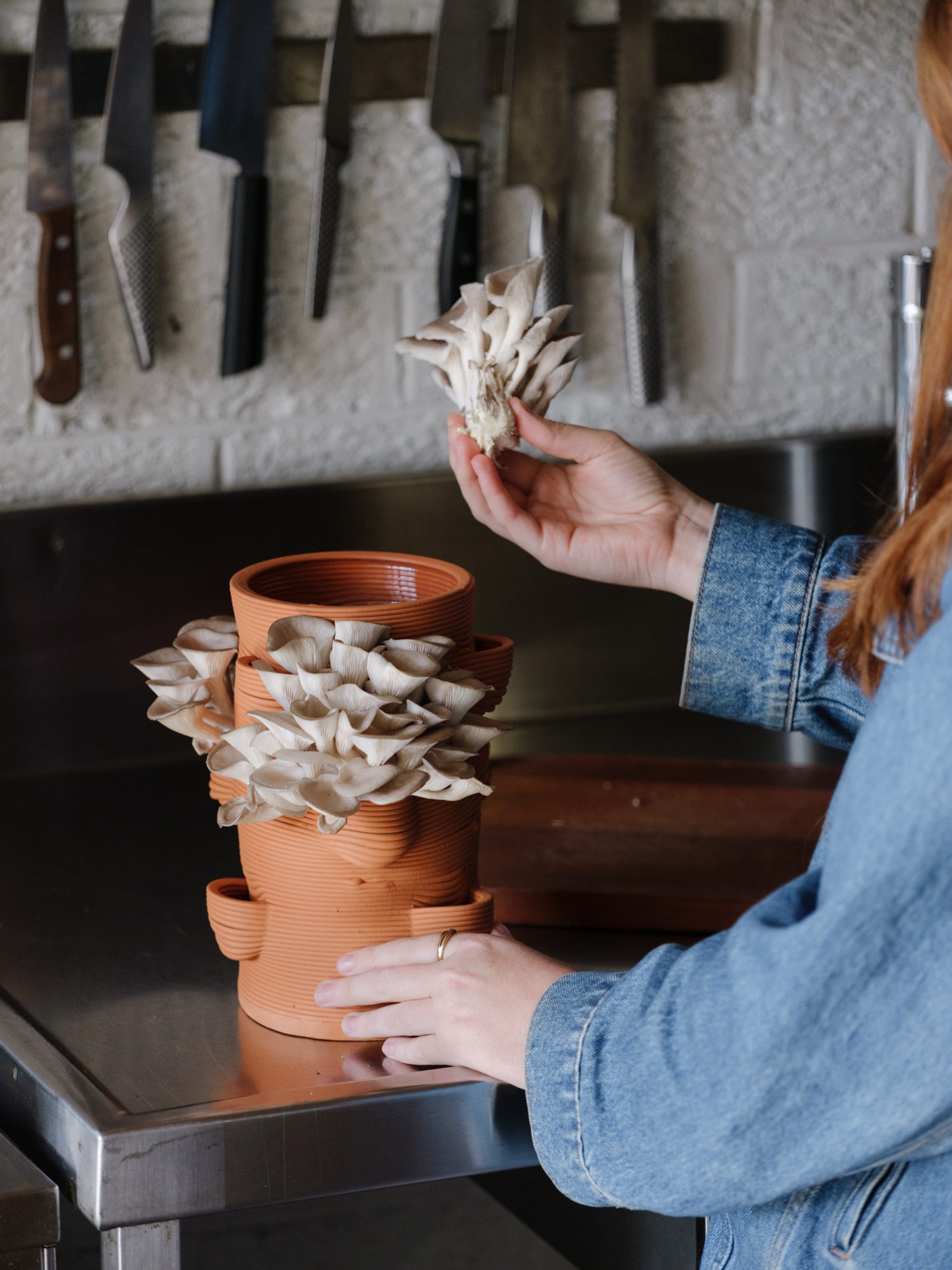
Fungi networks
AH: How does fungi inspire your practice?
CD: Many fungi have a web-like structure beneath the surface that holds soils together. They have a symbiotic relationship with trees that allows them to communicate and share nutrients. They spread and grow, continuing to branch out to create that web structure. I’ve always viewed that as a sustainability framework. The fungi network has been compared to Earth’s internet.
It’s hard to articulate how to move like fungi. In my brainstorming process — doing a mind map and just allowing that to continue branching out — you start with an idea and build on it. It’s the same in the design process. You’re making these iterations. You have one version and then you might change one thing in the ceramic 3D-printing process with a specific intention, but you can’t be certain how it will manifest. It’s just that way of thinking, continually growing and making new connections. It’s how I’ve tried to work with partnerships and the people I’m connecting to also.
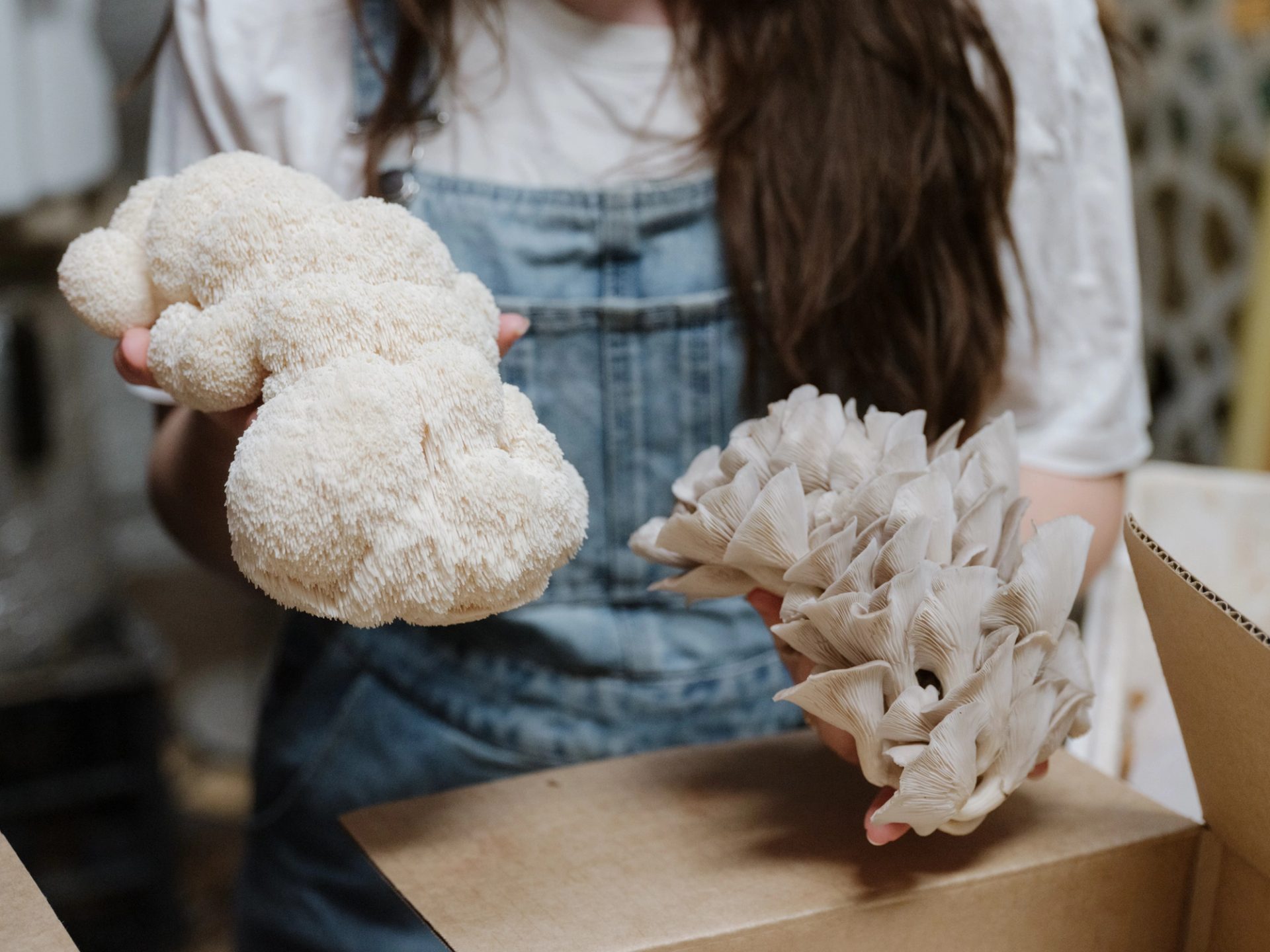
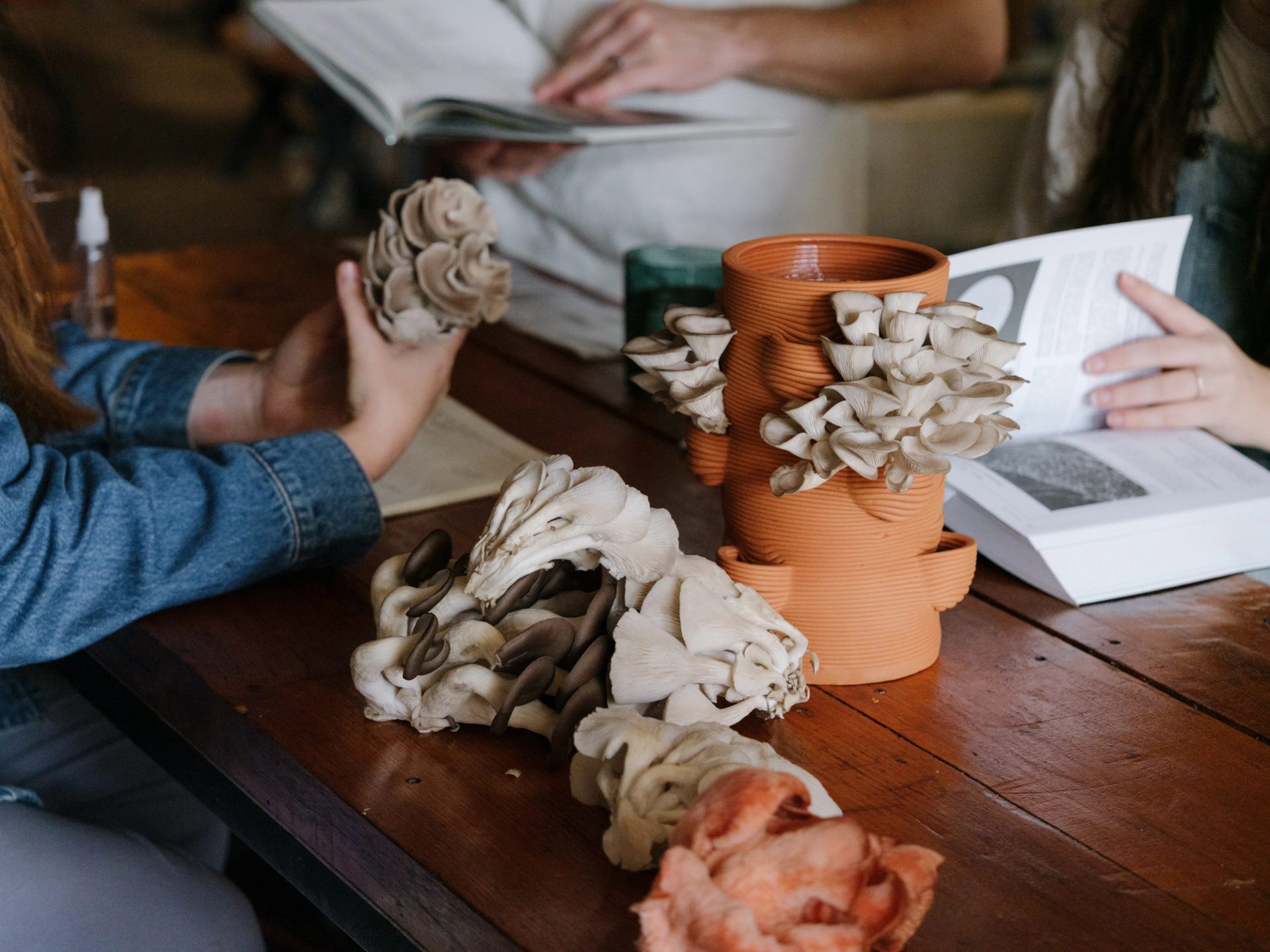
AH: How did the program influence your process?
CD: Through university I developed this narrative that to be an industrial designer I had to mass-manufacture goods in a factory elsewhere. This program has allowed me to develop my skills to be the maker too. If I think about it, this is all I have ever wanted to do — to use my hands to create and make things.
I’ve had to learn trust and patience in the whole design process. I am so much further ahead in a way that I wouldn’t have been able to imagine or visualise — it’s been this process of building my skills, learning, building assets and processes that continue to inform the next version.
There was a lot of perspective shifting and trusting that I was doing enough at every single stage. I had to make decisions, let go of directions and just be really clear on what I was working on at each stage and to focus on that. It was great having both the ceramic and plastic printers because I was able to rapidly prototype whenever I needed to. So that allowed the project to evolve.
AH: Were there any failures?
CD: I did have some contaminated substrate when I did my first testing and so that brought up [doubts]: Oh, does it not work? But that was where I connected with the local mushroom growers to validate what I was doing. That felt really good to connect — that was a turning point.
I’ve had to get better at the ceramic 3D-printing process to avoid things like cracked bases, air bubbles and rogue tool paths. I was able to make it better and iterate again, acknowledging that’s part of the process — that there’s going to be lots of failures. This is expected, and as designers we plan failures into our design process. It’s never wasted time, just information for the next one.
Sustainable design practices
AH: How important is sustainability?
CD: I have been thinking about sustainability through the entire process. It weaves in and connects with user experience, costs, processes and materials.
The mushroom grow process is inherently more sustainable than other food production methods. This is through the sourcing of substrate from waste streams, the lower energy intensity of the cultivation process, and in post-use where the substrate can be used as garden fertiliser. It doesn’t just go back into the earth; it nourishes soils and provides nutrients.
The design is aimed at beginner and entry-level mushroom growers, so creating the most foolproof design was key. I tested a variety of substrate methods and ideas including no-bag options, a reusable cup, plastic bags and also biodegradable alternatives. A standard bag was chosen to reduce contamination and simplify the user experience. The goal is to eventually transition to biodegradable bags.
I considered the energy inputs and outputs for the mushroom substrate and the terracotta system at each stage of the product’s life cycle. Ceramic is durable and long-lasting — a high-value item that I hope people will use and treasure. In the making process, the leftover clay can be recycled and turned into reclaimed clay.
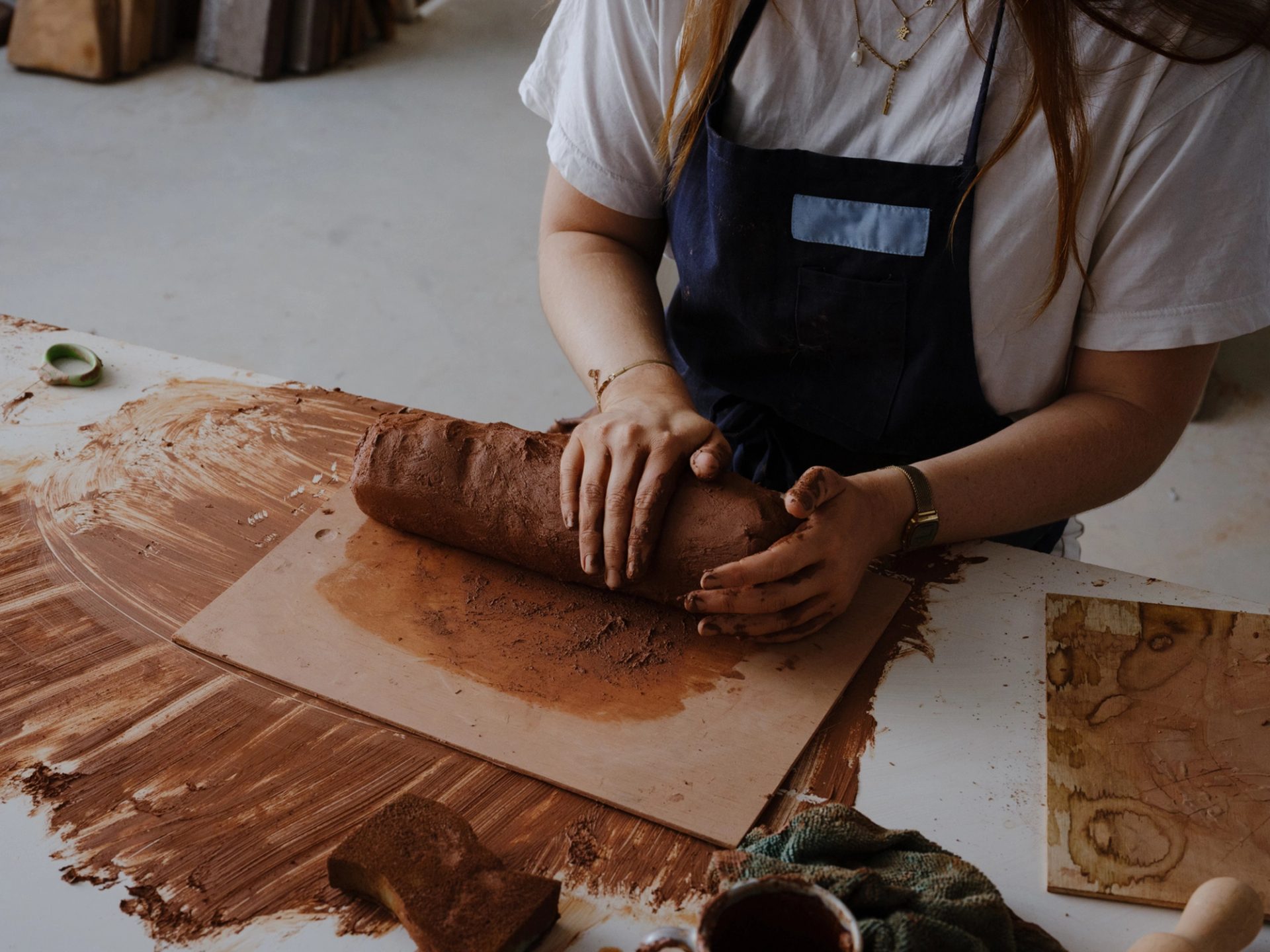
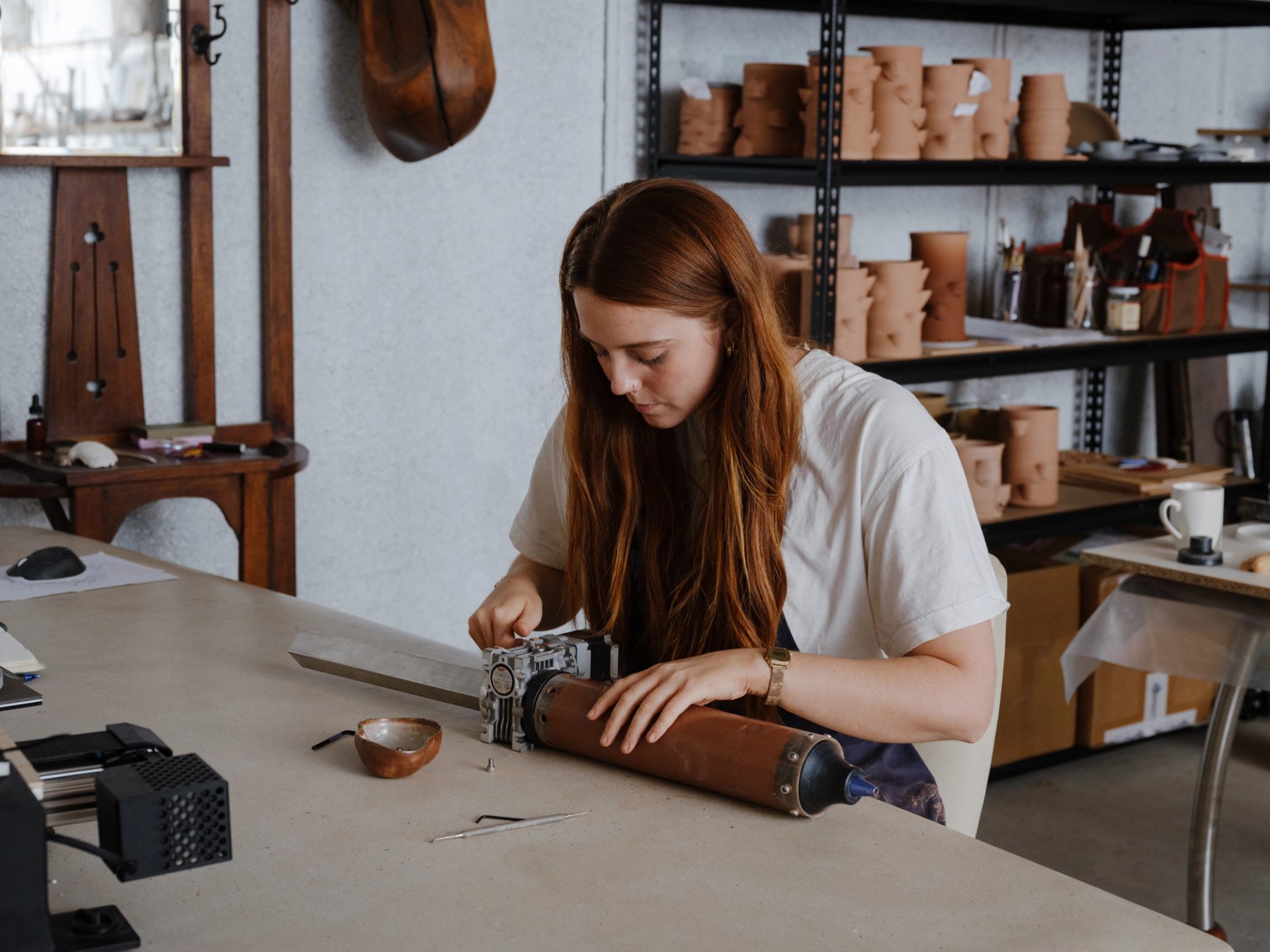
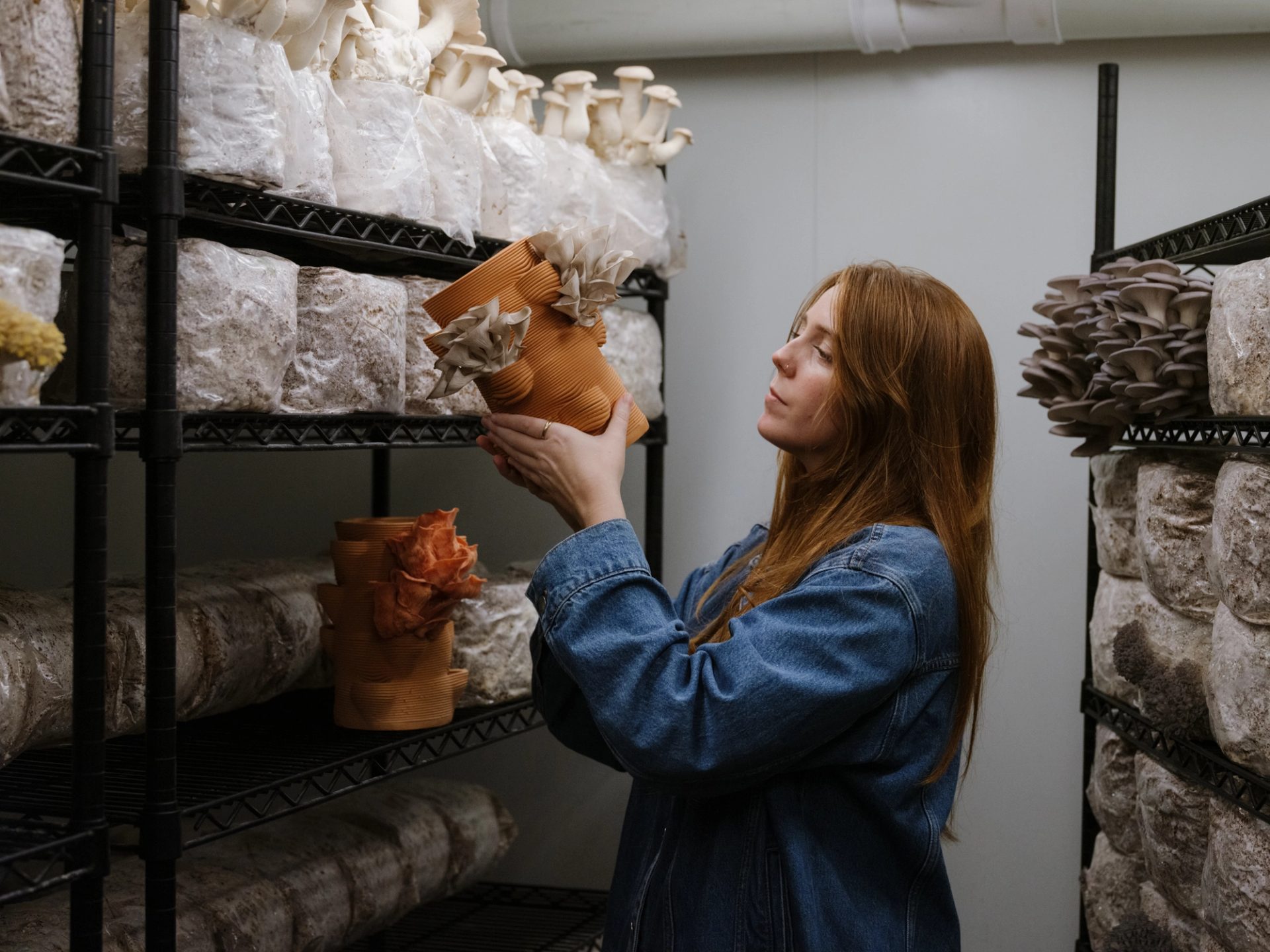
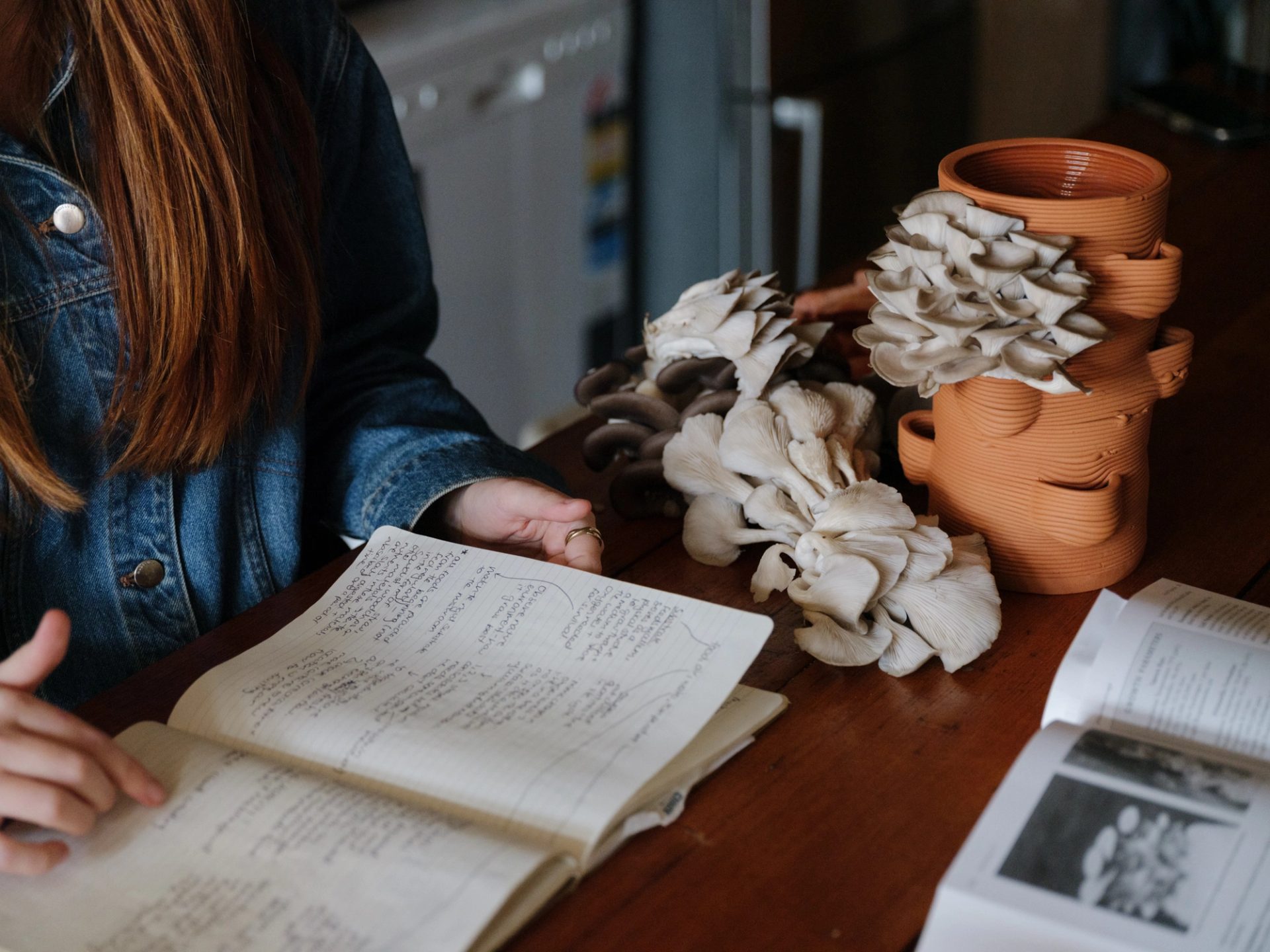
AH: Tell us about the mentoring process during the program.
CD: Ed was an ally on my team — it felt so good to be able to bounce ideas with him. He always brought in that lens of coming back to the user; that very industrial design thinking about the needs of the person using it.
[Industrial designer] Adam Laws was amazing. He shared some very practical examples of different projects he’s worked on and their impact. It was this beautiful business lens of thinking more about the volume you produce and how it’s positioned.
Spending time in the Design Futures Lab at UNSW was a big help for my whole project. It took quite a while for the printer to come and I was able to go into the uni to play with the ceramic printer and get totally re-educated on everything. Nichola Jephcott in the lab is a wealth of knowledge and very generous in sharing this.
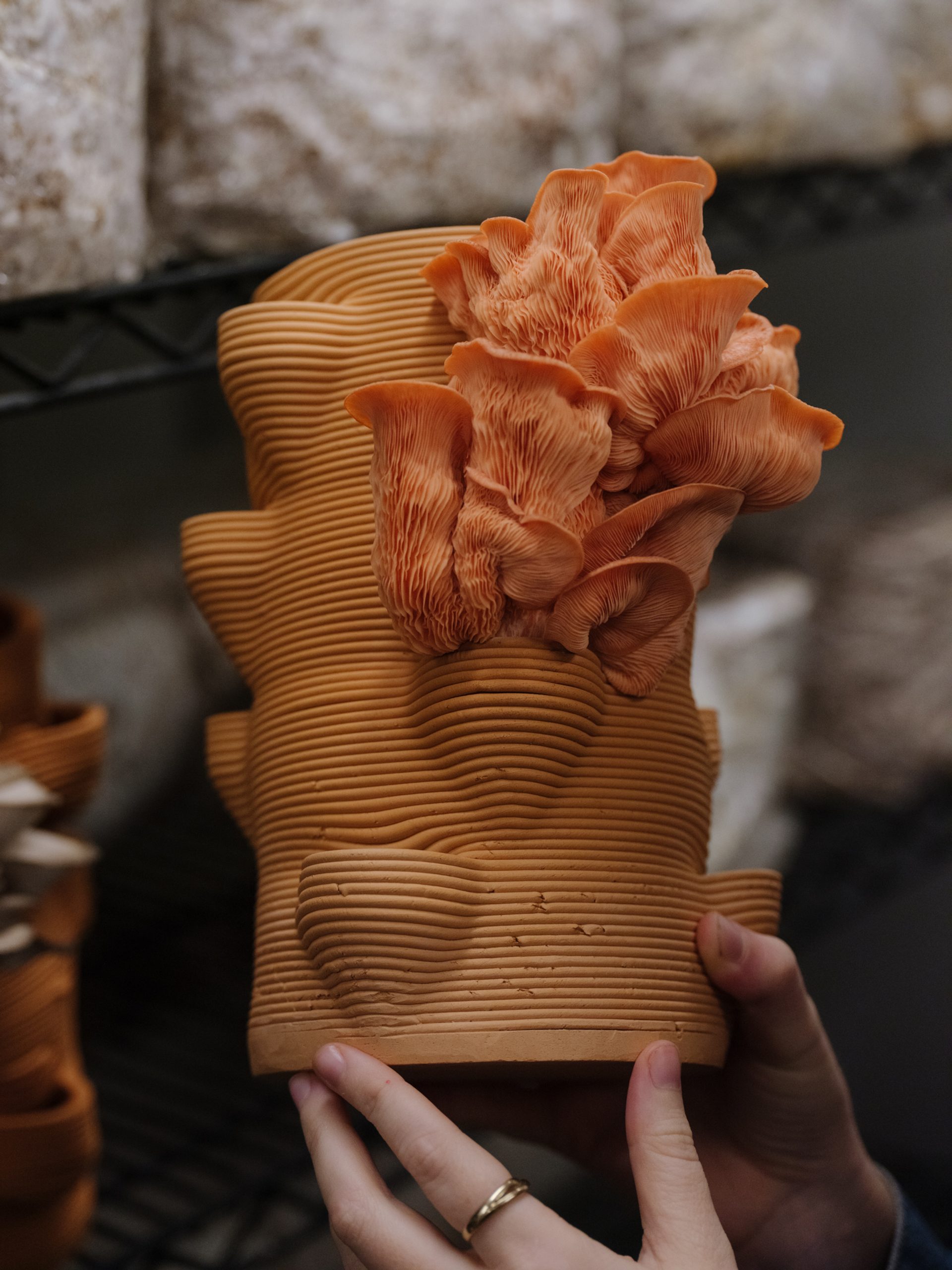
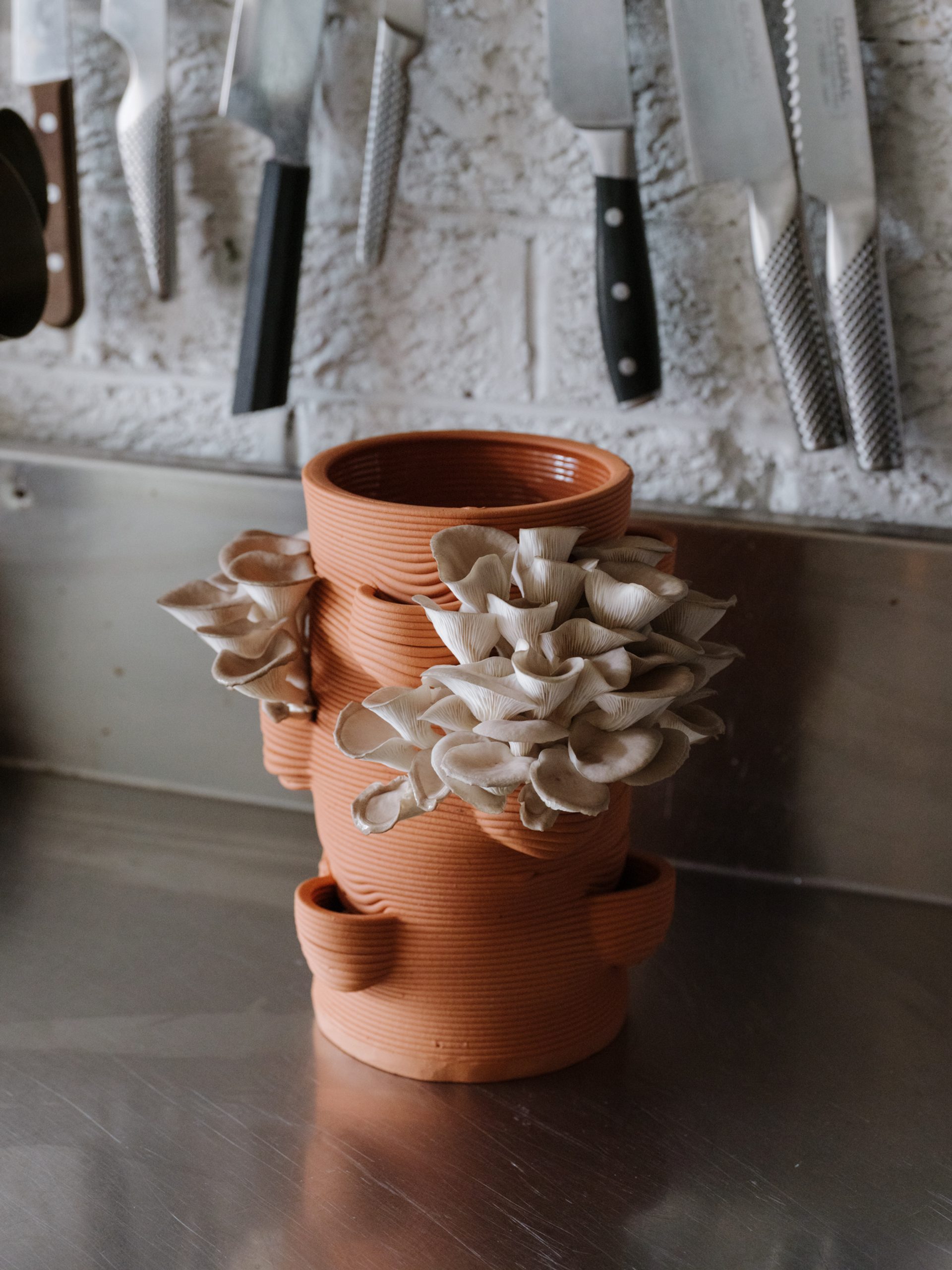
International opportunities
AH: What were some of the surprising things you learnt?
CD: One thing that changed was my idea of needing to be an expert at everything. As industrial designers, if we work on a project, we’re immersed in that topic and must become knowledgeable really quickly. When I was beginning, I had a lot of fears that I didn’t know enough about mushroom growing. But through the whole process, I realised that I actually know so much more than I thought I did.
Having the program behind me made me feel more confident to reach out and connect with people. I was thinking, ‘Oh, I’m really going all in with this creative project, so let’s make the most of it and go for it.’ That’s really motivating and has helped to get things done. The program gave me those support structures.
AH: Where do you see your future opportunities?
CD: I am in conversation with Studio Lafer, on behalf of German restaurant Käfer, about featuring Mycelia House as part of a new culinary experience in Munich. I am sending them a prototype for an upcoming launch event. It’s a really exciting opportunity.
My goal at the beginning was to sell Mycelia House to everyday people. I’m almost at that stage where I have a complete product to scale the making process to sell to individuals. I plan to upgrade my ceramic printer and evolve the making process.
In the future I see Mycelia House as a ritual object in the home that you tend to and build a relationship with. I hope it contributes to a future where we grow our own food at home, and that this will evolve to growing locally within our communities.
I feel so grateful for having this time to work on something I love. This program has allowed me to set up a process and something I can keep building on, thinking of it long-term rather than short-term.
An annual initiative supporting Australian industrial designers working in sustainable design.
Applications Closed
Next Open May 2026
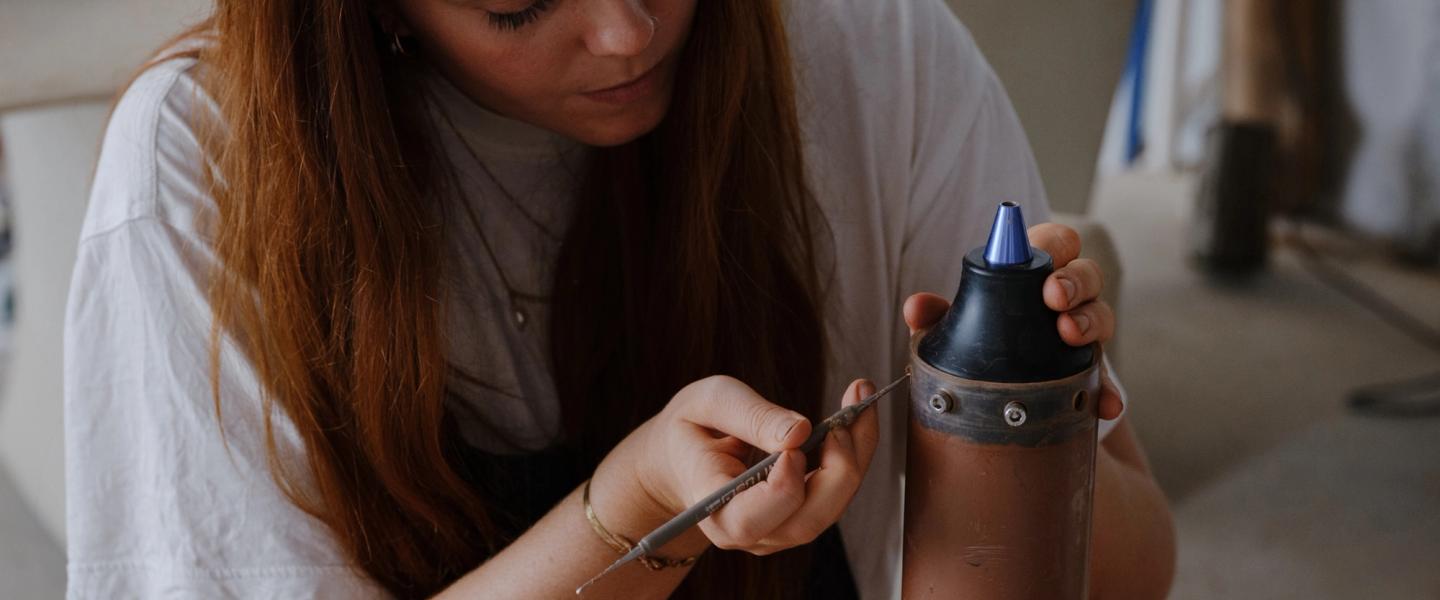
Carl Nielsen Design Accelerator
The annual Carl Nielsen Design Accelerator, supported by a generous bequest from Carl and Judy Nielsen, recognises achievement by Australian industrial designers working in sustainable design. Powerhouse will select one project designed in Australia that demonstrates outstanding design for sustainability.
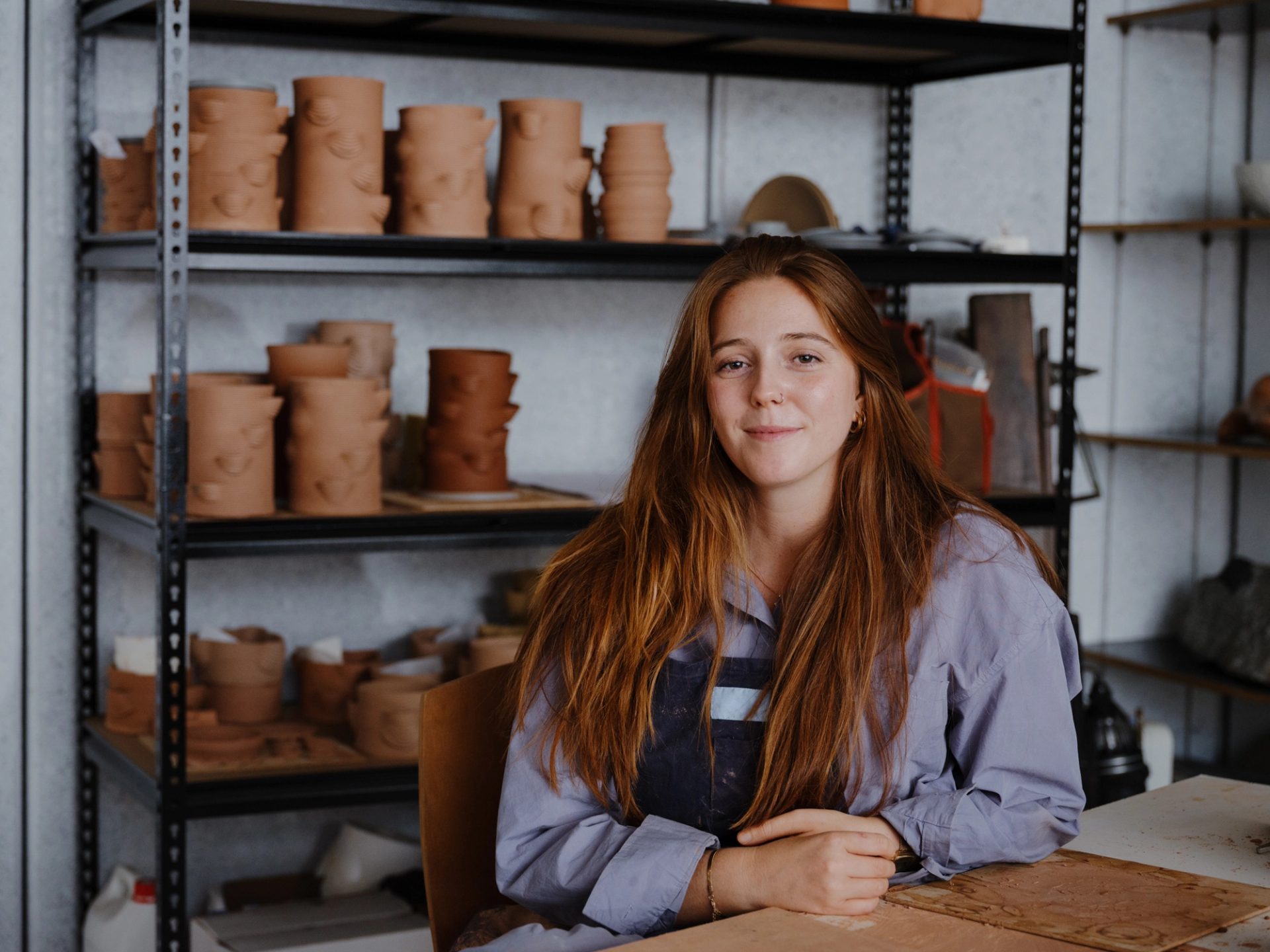
2024 Recipient
Caity Duffus is a Sydney-based designer with a background in industrial design, graduating from UNSW with Honours in 2020. She has since developed her expertise in photography, videography and branding to collaborate creatively and express ideas. At Vert Design, she has honed her skills in copywriting and visual communication. Central to all her work is a love for sharing stories and translating information, ideas and experiences in new ways.
Mycelia House by Caity Duffus is a functional container and cultivation system that showcases the beauty of oyster mushrooms and supports an ideal environment for them to be grown within the home.